If you notice cracks in your concrete foundation or basement walls, you will likely use one of two repair methods. The first is epoxy resin injection the second is polyurethane foam injection. In theory, the execution of these techniques is similar; however, each has qualities best suited for specific repair jobs. To help you better understand the properties and uses of each, here is a breakdown of epoxy resins and polyurethane foams. But before getting started, there are a few questions that you should consider:
- Is the crack structural/ do you need to restore structural strength?
- Is it active or dormant?
- How much moisture is present?
- Is the crack actively leaking?
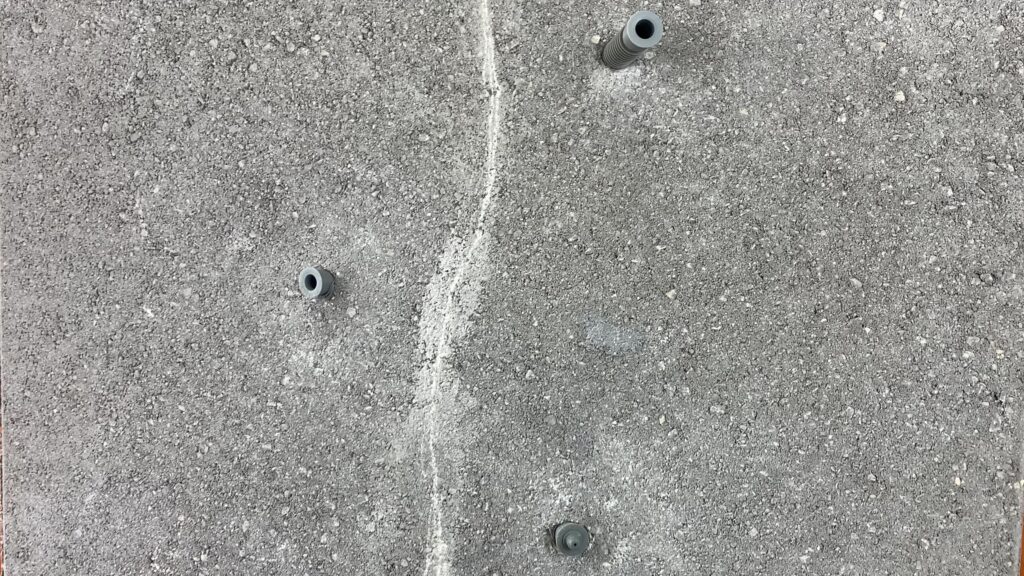
But first…What are epoxy resins and polyurethane foam resins?
Epoxy and polyurethane resins are chemical products commonly used to fill and seal cracks in concrete. These resins often require a mixture of 2 components (sometimes 3), each with specific reaction profiles and physical properties.
Epoxies are adhesives with varying viscosities that typically do not expand. As it cures, the epoxy creates a bond with the concrete equal to or greater than the original tensile strength of the concrete. Epoxies first cure over a specific amount of time (from minutes to hours) and will continue to harden over the days and weeks following the injection.
Polyurethane foams are generally water-activated sealants that expand when they come into contact with water. They often require an activator or an accelerator that you mix with the polyurethane product before injection. Since they are hydro-active, polyurethane foams are the perfect solution for leaking cracks.
The ability to inject either of these into cracked concrete makes them a more precise repair method than others. However, their individual properties make each product unique, so let us look at when and why you might choose an epoxy resin vs. a polyurethane foam.
Epoxy Resin
For structural repairs with little to no moisture surrounding the crack, epoxy resin is likely the solution you need.
Characteristics:
- Structural repairs – The tensile strength of cured epoxy is typically equal to, if not greater than, the tensile strength of concrete. This detail explains why contractors generally choose epoxy resin for structural concrete repairs. After curing, epoxy resin is usually rigid, making it the best option for dormant concrete cracks.
- Curing time – Epoxy resin can take up to several hours to cure and continues to harden over the days and weeks following injection. This longer curing time gives the epoxy time to penetrate the concrete and reach the heart of the crack. Epoxy resin is available in varying viscosities depending on the crack width. The viscosity and crack depth can impact drying and curing time.
- Environment – For epoxy to properly adhere to the concrete, the crack, and surrounding environment should be clean and dry. If the concrete surface is wet (but not leaking), the epoxy may not adhere as well to the concrete. For actively leaking cracks you will need to use a polyurethane foam resin.
- Injection technique – Epoxy resin injection typically requires surface ports or injection packers. If using surface ports, the concrete surface must be dry. Moisture can weaken the bond between the epoxy used to glue the surface ports on the crack. If the bond is too weak, the epoxy holding the port in place will not withstand the injection pressure. Do not remove the surface ports (or injection packers) before the epoxy has cured.
Learn about the epoxy crack injection method using MABI injectors.
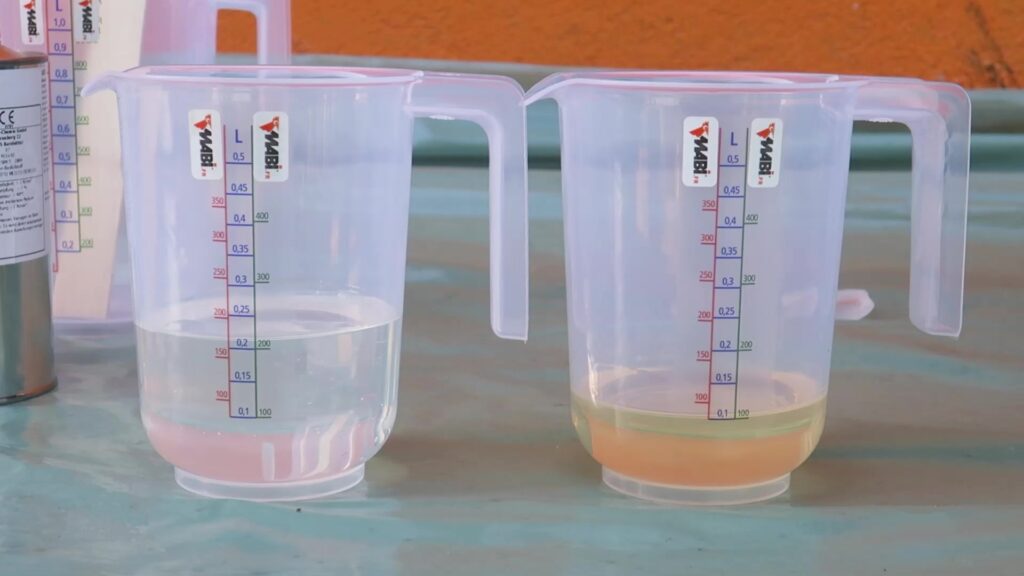
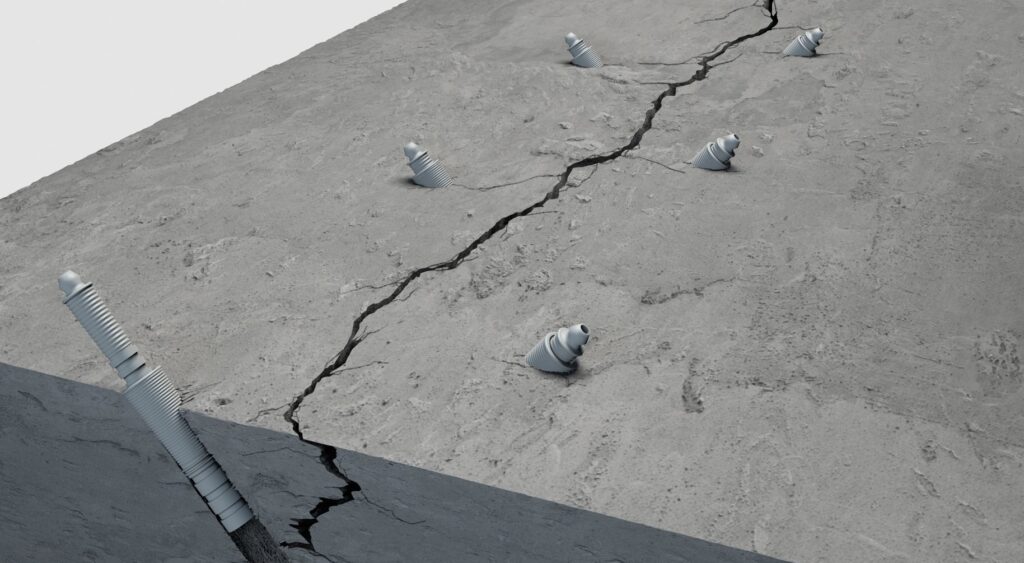
Polyurethane Foam
Many polyurethane foams react when in contact with water; therefore, this method is standard for underground construction and leak sealing. However, there are two different types of polyurethanes, hydrophobic and hydrophilic. The former repels water, while the latter mixes with water. Because they expand, polyurethane resins typically require higher injection pressure.
Characteristics:
- Water stop applications – Since polyurethanes are generally hydroactive, they are ideal to use regardless of the condition or state of the crack. More importantly, polyurethane foams can seal actively leaking cracks. The expanding nature allows the polyurethane to squeeze into the voids in the concrete. Polyurethanes can grow anywhere from 2 to 40 times their original volume.
- Curing time – Polyurethane foam needs much less time for the curing process. When polyurethane has finished the curing process, it creates a more flexible bond (compared to epoxy). This flexibility helps accommodate any potential movement in the crack or joint caused by the surrounding environment. A flexible bond means polyurethane creates a less structural bond with the concrete and is less reliable for structural repairs.
- Environment – Polyurethanes are acceptable to use in wet and less favorable conditions. They do not require a dry surface or the crack to be entirely clean. (Although it is best to clean out the crack before injection when possible.)
- Injection technique – To push polyurethane foam into narrow cracks and to fill any potential voids, you’ll need to use higher injection pressures. High-pressure injections will ensure that the product goes where it needs to, especially in the case of active leaks.
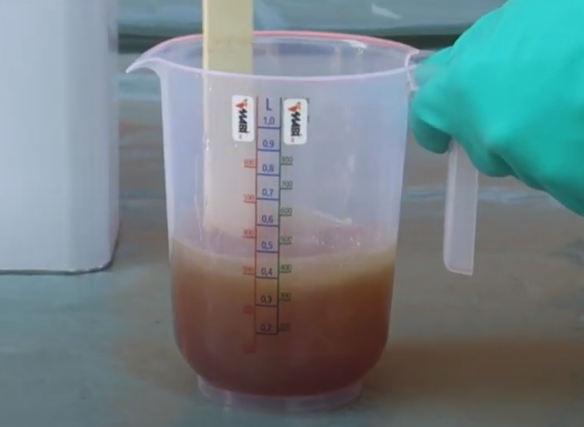
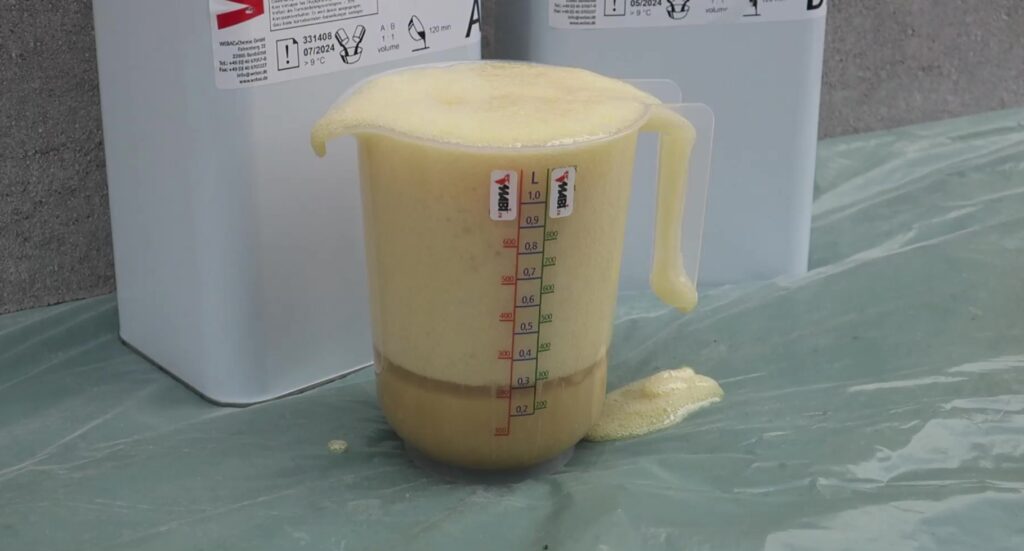
Epoxy vs. Polyurethane in a nutshell
Epoxies are great for structural repairs where little to no moisture is present. They take longer to cure but result in a rigid adhesive that can restore tensile strength. Epoxy injection does not always require drilling as you may choose to use surface ports.
Polyurethanes are more suited for non-structural water-related repairs. They can either be hydrophobic or hydrophilic, each type with specific applications. Polyurethanes have a much shorter curing time than epoxies and yield a more flexible bond once cured.
Note: Regardless of the product, we advise reading the TDS (technical data sheet) before using any epoxy or polyurethane.