How to seal leaks in concrete with polyurethane resins and MABI injectors?
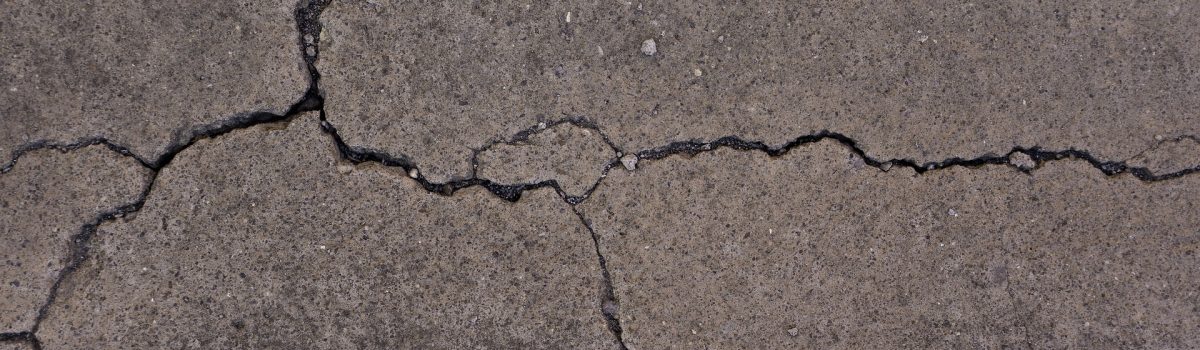
If your crack is actively leaking or surrounded by an unfavorable environment, the polyurethane crack injection method is likely your best solution. This repair method is ideal for wet and dry applications, regardless of the crack size and condition; however, there is no such thing as a universal solution, so before choosing your injection method, consider the following questions:
Is the crack structural?
If the crack is structural, polyurethane is not the right choice. Polyurethane resin is perfect for many situations and varying applications; however, it does not possess the same structural strength as epoxy resin.
Is it active or dormant?
As their name suggests, active cracks may move or change over time. When cured, polyurethane foams can be flexible to semi-flexible, allowing them to accommodate slight movement in the concrete.
How much moisture is present?
Wet or dry, clean or full of debris, polyurethane foams are ideal in many environments. More importantly, many polyurethanes will actually react upon contact with water making them optimal regardless of moisture levels.
Why choose MABI Injection Packers
With an all-in-one design, MABI injection packers were developed with contractors in mind. Molded out of a high-quality, resistant plastic, we’ve added the fitting directly on the injector so you don’t have to. They’re ideal for low to medium pressure injections and can be used with a variety of chemical products for your concrete repair needs.
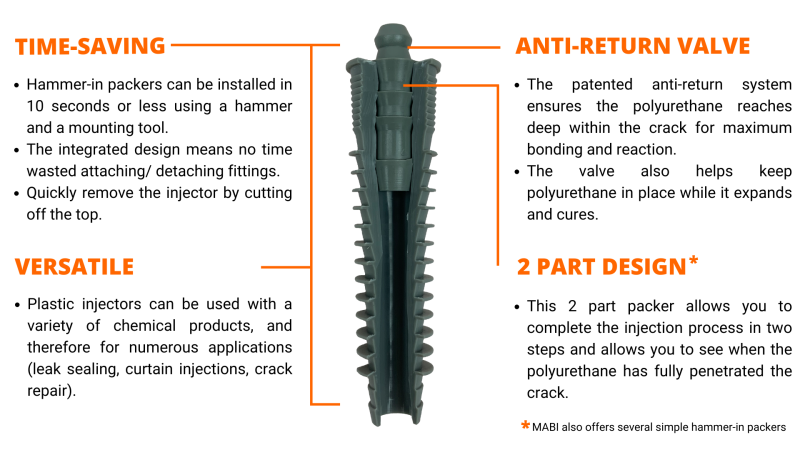
WHAT IS POLYURETHANE FOAM RESIN?
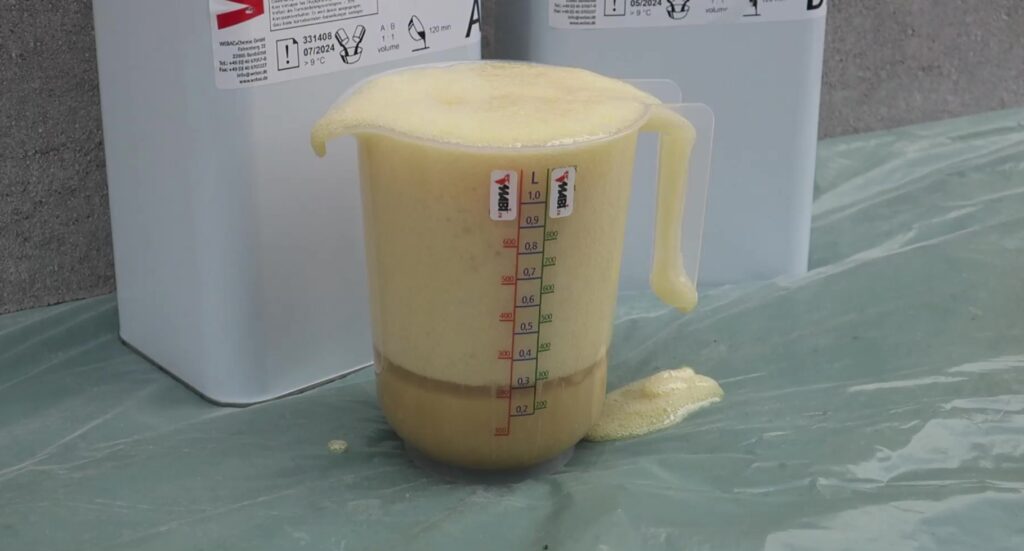
Polyurethane resin is (typically) a water-activated chemical product that expands when it comes into contact with water. The ability to expand makes PU perfect for leak-sealing and void filling. Polyurethane resins usually require an activator or accelerator that mixes with the polyurethane before being injected. Once cured, they create a flexible to semi-flexible bond and a resistant, long-lasting seal.
Some polyurethanes are hydrophobic, meaning they repel water, while others are hydrophilic, meaning they mix with water. These different polyurethanes have different applications based on their reaction to water. Hydrophobic polyurethanes (foams/ resins) are ideal for crack injection and joint voids, and hydrophilic polyurethanes (foams/ gels) are for curtain and bladder injections. As always, assess the type of repair needed for the crack in question before choosing the appropriate PU.
The Polyurethane Injection Method
Polyurethane usually requires higher injection pressures, needing slightly different equipment and a different injection method. You will want to use injection packers (hammer-in or mechanical) that can withstand higher pressure injections rather than surface ports. The type of injection packer and the intended application will determine the specific steps required.
Here is how to perform the polyurethane crack injection method using MABI hammer-in injection packers:
Step 1: Preparation
Remove any loose dust or debris using a wire brush or compressed air. This step will allow you to assess the crack and determine if polyurethane repair is suitable. Although polyurethane can be used even in adverse conditions, starting with a clean surface is best when and where possible.
Step 2: Crack evaluation
Check the state of the crack and verify the presence of humidity or water if it is not already apparent. At this point, you can determine the best course of action, including what polyurethane to use and where to place injectors.
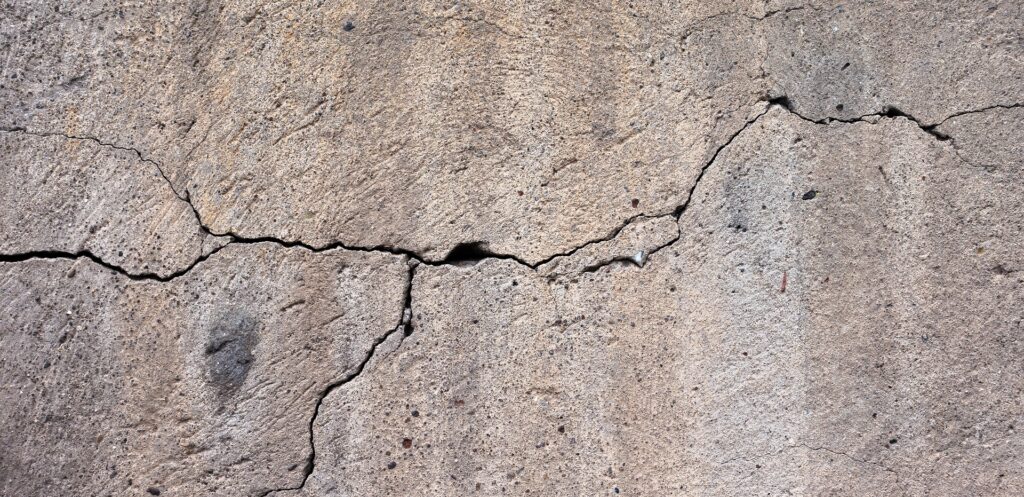
Step 3: Drill holes
Before drilling, measure and mark where to place injection packers. Drill the holes at regular intervals on either side of the crack. To determine how far apart to space the injectors, divide the thickness of the structural element by 2. For example, 12 in. wall → 12/2 = 6 in. Drill holes at a 45° angle into the crack so the injectors intersect the fissure at the midpoint of its depth.
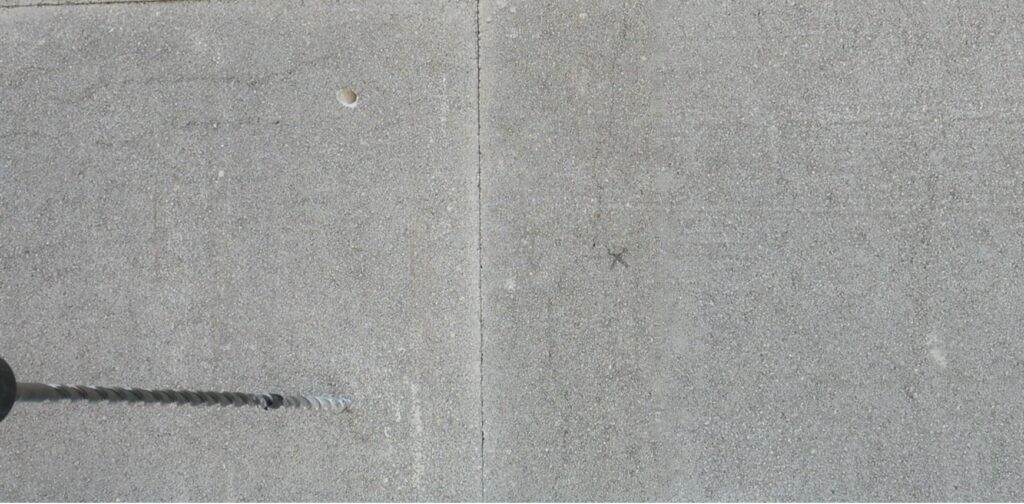
Step 4: Injector installation
Before installation, use compressed air to remove the remaining dust from the drill holes. Install MABI hammer-in packers with a hammer and mounting tool. We designed the mounting tool to help install the injection packer without damaging the zerk fitting.
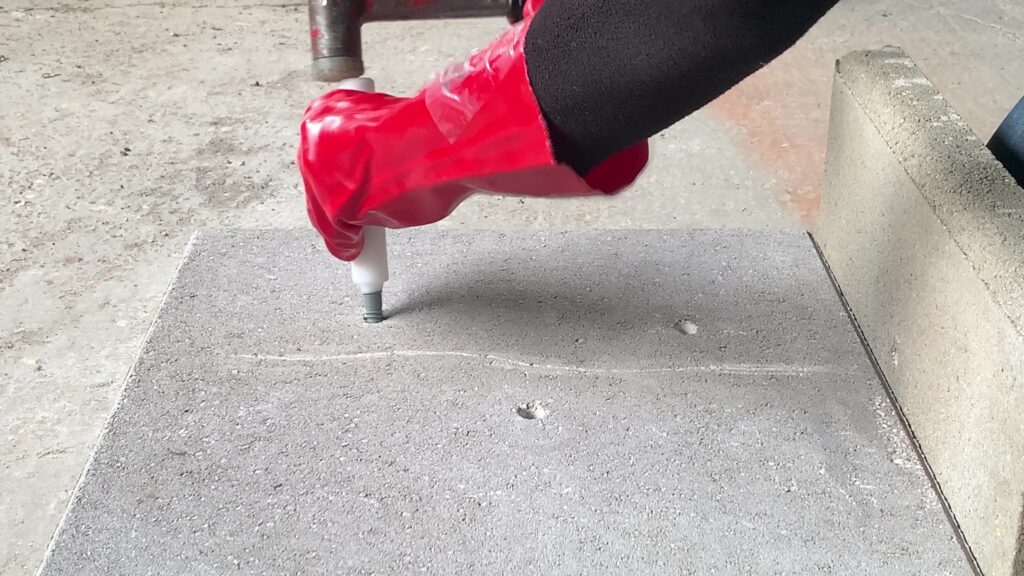
Step 5: Foam injection
Prepare the polyurethane by mixing the necessary elements per the manufacturer’s instructions. Starting from the bottom (or lowest point) of the crack, working your way up, inject your polyurethane until it is visible from the face of the crack, and in some cases, the following injectors.
Step 6: Expansion and curing
Since most polyurethanes are hydro-active, they will begin to expand upon contact with water. Allow the polyurethane to fully expand (2-40 times its original volume) to fill the cracks and spaces in the concrete. Initial curing time can take minutes to hours depending on the polyurethane.
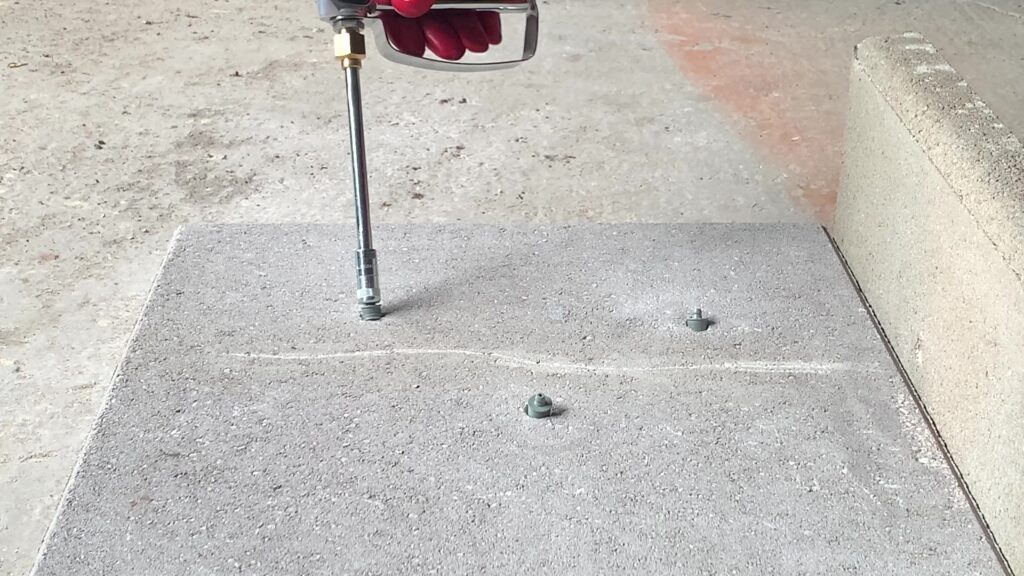
Step 7: Packer removal
Once the foam has fully cured, remove the injection packers. If using MABI hammer-in packers, you can easily cut off the protruding part with a small ax and hammer.
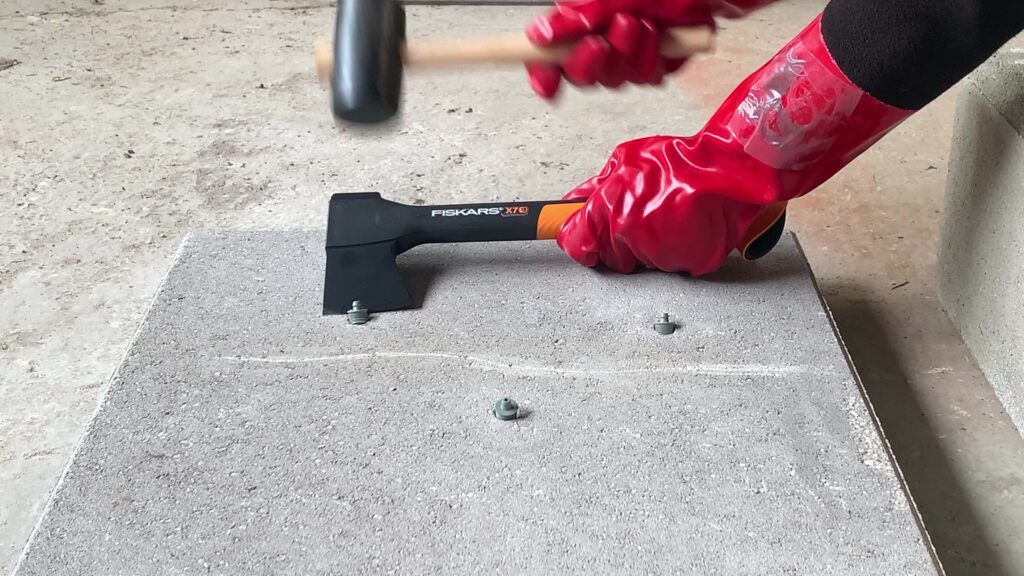
*If you are using our high-pressure injection packer (ref: 01090050), there is no need to wait for the foam to cure. The no-return valve inside the injector body (rather than the head) will hold the product in place.
Learn all about MABI injection packers for concrete repair and leak sealing here.
To order MABI injection packers become a US distributor, contact us!